Safer Paper Production with a Highly Automated Winder
Raumaster Paper has delivered a highly automated winder to the Melitta Group’s mill in Minden, Germany. The winder is designed to produce narrow rolls of filter paper, featuring specially automated functions for core feeding, end gluing and roll weighing. One of the main criteria for the new winder was ensuring operator safety.
The Melitta Group’s story began in 1908 with the invention of filter paper, and Melitta coffee filters remain the company’s core product to this day. Since then, Melitta filters have undergone continuous development, with ongoing modernization of production processes. To support this development, Raumaster Paper provided a highly automated and safer winder solution, tailored to fit the mill’s limited space.
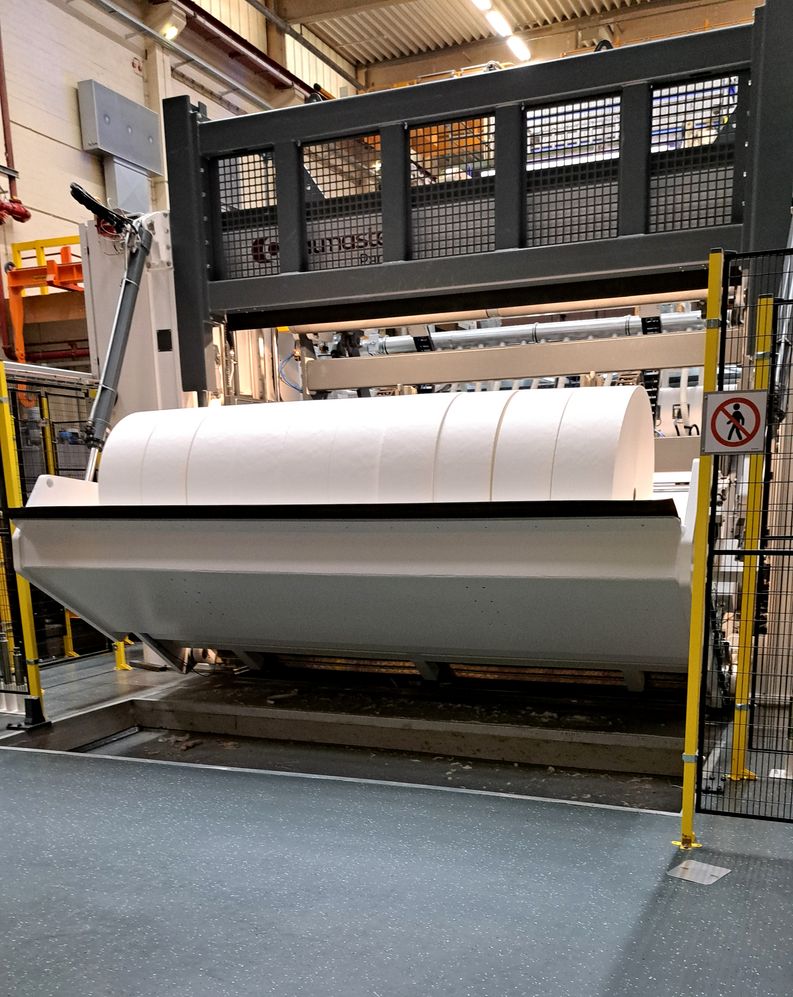
Safety first
With over 100 successful winder project deliveries worldwide, Raumaster Paper has a dedicated team focused solely on winding processes — covering mechanics, automation, safety, and user-friendly operation.
“Safety is now one of the main priorities customers seek to upgrade or replace their machinery,” says Gerhard Gabriel, Sales Representative for Raumaster Paper.
The Melitta winder was designed to reduce manual operator interventions, enabling the entire winding process to run automatically from start to finish.
“During operation, the operators don’t need to access the machine. Instead, they monitor and control the winding process safely from outside the safety barriers using operator software on touch panels,” explains Andree Peperkorn, Production Manager paper manufacturing at Melitta in Minden.
Raumaster Paper’s winders are highly automated, with features such as automatic web threading through the slitter section, fast and accurate slitter positioning, and fully automatic core in-feeding with gluing. Fast set change enables high production capacity. With traversing end gluing, the operator can just send the finished rolls to wrapping.
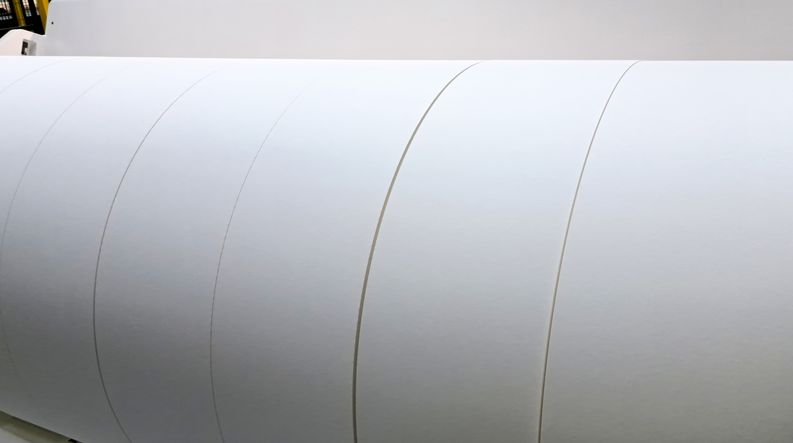
Special features
The Melitta winder was developed in close collaboration with the customer to meet their specific production requirements. Filter paper has high surface friction, requiring a precise winding process to protect the paper’s structure. This requires for extremely accurate tension and drive control.
Testing is an important part of Raumaster Paper’s production process. The entire winder was pre-assembled at Raumaster Paper’s production facilities and tested using Melitta’s actual material.
“Testing ensures a smooth and efficient commissioning phase, optimal winding quality, and gives the customer the possibility to see the machinery in action before delivery,” Gerhard Gabriel notes.
Raumaster Paper’s winder team integrated several special functions into Melitta’s winder an integrated web inspection system, efficient dust extraction and an edge trim handling system. To fit the limited space, a special scale system was integrated before roll releasing. The automatic core in-feed was designed specifically for narrow cores.
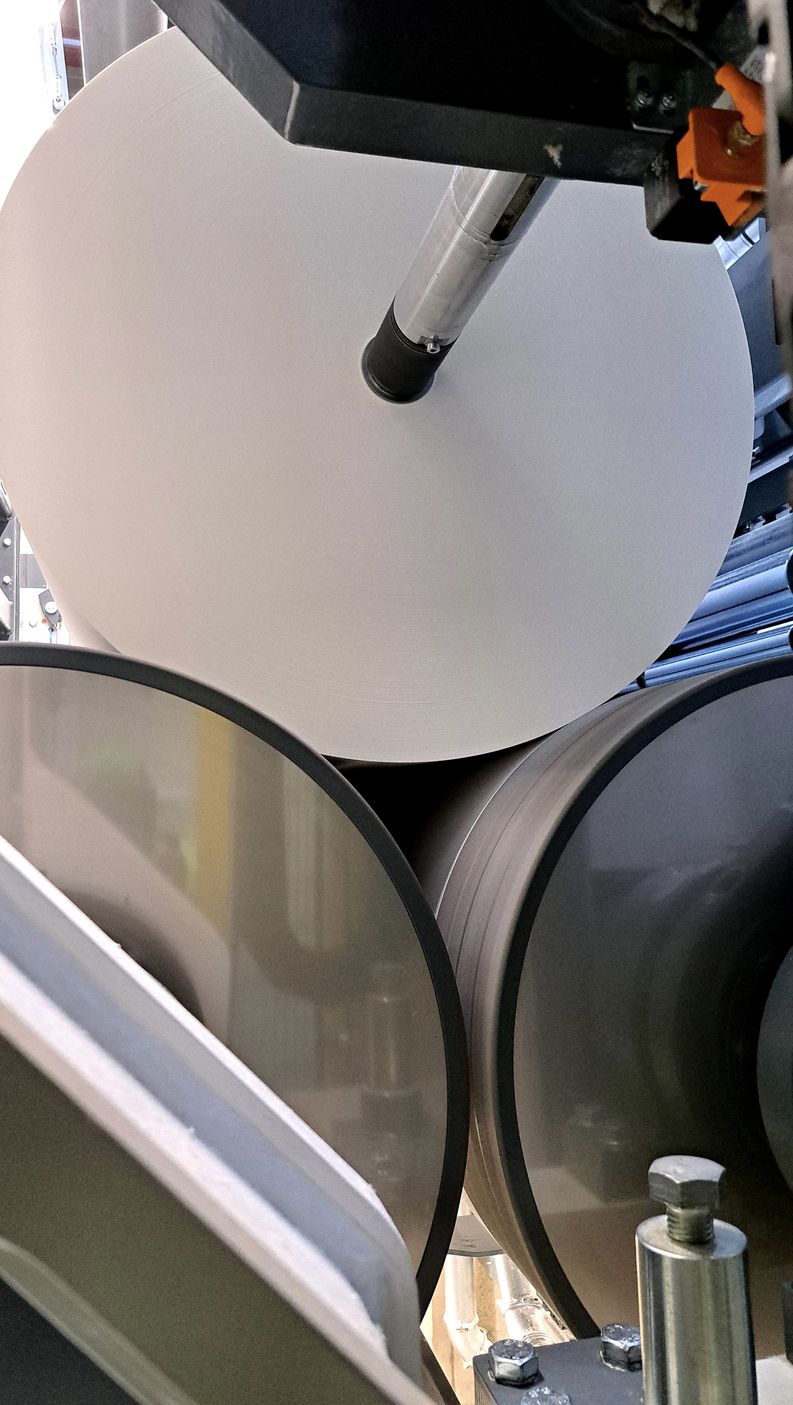
Remote operation and support
Raumaster Paper’s TIA Portal control system enables a single integrated platform for both drive and machine controls, including full diagnostics for each equipment. This benefits both daily operations and maintenance. With Raumaster Paper’s remote support and customer service, the team remains available to assist Melitta after the project’s completion.
“The ability to access the winder system remotely means our customers can always count on quick assistance from Raumaster Paper, also after commissioning,” says Gerhard Gabriel.
“Raumaster Paper has proven to be a well-coordinated team with extensive experience, from order placement to design and implementation. This gives us confidence in their ongoing support for the project,” concludes Florian Meyer, Project Engineer at Melitta.